- Erection of scaffolding and storage tents for parts and consumables.
- Construction of weather hoods to protect the gas turbine enclosure once their enclosure was disassembled.
- Transfer of spare parts from the off-site stores to the temporary storage tents.
- Changing of air intake filters.
- Completion of maintenance activities that could be reliably completed outside a unit outage.
Despite the Global Covid Pandemic, ESB International successfully project managed and delivered major scheduled outage works at the Delimara 4 power plant in Malta.
ESB International provides Operation & Maintenance (O&M) Services at the Delimara 4 power plant Marsaxlokk, Malta. The plant is owned by ElectroGas Malta (EGM), is the first Independent Power Producer in Malta and provides highly efficient, clean, and reliable energy for the Mediterranean island nation.
Delimara 4 is a 215MW Combined Cycle Gas Turbine plant, consisting of 3 x Siemens SGT-800 Gas Turbines, 3 x Aalborg HRSGs and 1 x Siemens SST-900 Steam Turbine. ESB International employs 39 people at the site as part of the O&M team with technical support from ESB International Head Office in Dublin.
In 2020 major outage works were scheduled for all three units that included Level B inspections (hot gas path) on all three gas turbines and the steam turbine, along with some significant remedial works on the balance of the plant. It was planned that works would be rotated to allow the plant to remain in operation whilst an adjacent unit was on an overhaul to meet commercial and Maltese power demands. Regrettably, the months of March through to July 2020 saw the initial Covid-19 lockdown restriction come into force affecting all travel to Malta. This meant that parts required for the outages could not be shipped to the site with any degree of certainty, and specialist labour necessary for the gas turbine inspections and other repairs could not enter the country.
Once restrictions were relaxed, the B Inspections began. These were project managed by the ESB International site team, who arranged spares, consumables, and maintenance contractors. Work on the gas turbines was led by a team of specialist contractors mobilised from the original equipment manufacturer based in Sweden who worked alongside ESB International and Maltese contractors to deliver the project successfully.
The Delimara 4 site has a small site ‘footprint’, and a wide variety of works had to be completed before the outages to support core outage activities. These included:
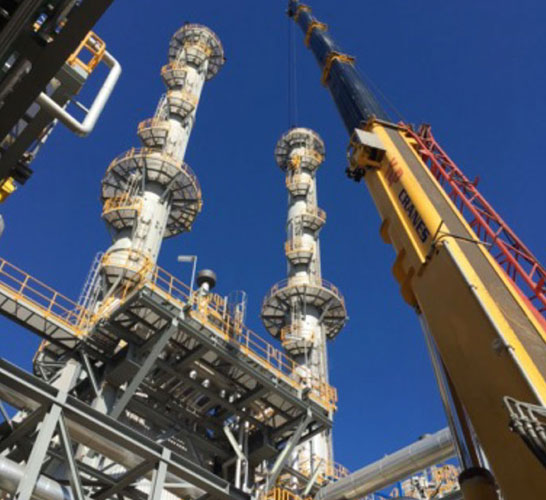
All work requirements had to be performed in accordance with normal site health and safety standards that were now compounded by strict governmental and site Covid procedures. For example, personnel involved in outage activities were subject to a PCR test at least every 14 days, and contractors travelling from abroad were required to isolate for 48 hours before taking a PCR test, regardless of any pre-travel PCR tests. Work parties on site were kept separate, the wearing of face masks was mandatory, and temperature checks were a feature of daily access to the site along with a 14-day quarantine for anyone identified as a close contact to a confirmed or suspected case of Covid. These additional procedures added greatly to the effort and planning required to complete the outages but were necessary to protect the health of all involved.
Each outage was scheduled to be completed within 22 days, and all were successfully delivered on time with no injuries or lost time incidents. There were a small number of positive Covid-19 cases identified on-site, but all originated from external contacts, and because of the stringent site access and social distancing procedures, there was no impact on the station's daily operations.
Despite the global pandemic challenges, all works were successfully completed to plan by the end of Q1 2021. The completion of this work means the plant can be expected to operate for the next 3-4 years before the next major inspections are due.
In summary, the success of this project was down to the hard work and rigorous planning of the ESB International team, close co-operation between the major stakeholders and the continued support from the Plant Owners, EGM.